Building is a key sector in Spain thanks to its size and its economic, environmental, and social relevance. Yet, while it holds a lot of weight, it’s still quite divided. With this in mind, in 2021 the Association of Real Estate Developers of Madrid (known as ASPRIMA) decided to unite a group of agents already working as part of the construction value chain to create what they called the Clúster de la Edificación (the Building Cluster) and they have been working towards a common goal ever since: creating better urban environments through innovation in all types of buildings.
The Cluster already has around 100 associated entities, most of which are large companies and SMEs, but there are also universities and research centres in the mix. “It was necessary to join forces and create synergies. There’s a lot of talent, but if we aren’t working together, it’s difficult for the innovation we are looking for to see the light of day”, says Miguel Pinto, the Cluster’s manager. One of the challenges the group has set for itself is to promote industrialisation in construction, something that Pinto assures us will define the future of the sector.
How do you approach the challenge of innovation and what strategies have you devised to incorporate it into the sector?
We’ve defined five strategic focal points for boosting innovation in the sector. They are industrialisation, rehabilitation, environmental sustainability, lean construction, and digital transformation. These are the five main areas that define our actions in the major fields of development in innovation.
The entities that form part of the cluster then break off into working groups – there are around twenty of them – to flesh out these five strategies. For example, in waste management, which falls under the environmental sustainability umbrella, there is a group of around ten companies that conduct research in collaboration with the Polytechnic University of Madrid.
And what progress is being made in lean construction?
This philosophy has been borrowed from lean manufacturing, [the idea of] being more productive when manufacturing an item. It came from Toyota’s production system in the automotive industry. [Toyota] hung the tools from the ceiling and made the process faster, thus saving seconds [during production]. ‘Lean’ just means adjusting the available resources and eliminating inefficiencies and waste.
Lean construction consists of optimising what adds value to a construction project and analysing how to eliminate what doesn’t. By applying this methodology on a construction site, processes can be improved from the moment the project begins in terms of safety, sustainability, or speed.
Ver esta publicación en Instagram
Is the industrialisation of building the key to development within the sector?
Yes, definitely. When we talk about industrialised construction, we are referring to a construction process that produces components, modules, or systems by means of industrial manufacture for the construction of a building. These elements are then transported to the construction site for assembly on site. But it’s not just about putting it all together in another place. It’s also about making the process more automatic, roboticized, and efficient by serialising and mechanising these elements in the factory.

What is it, then, that defines this system?
In terms of production and installation, the system is characterised by the fact that it’s carried out in a place that is not the construction site, [meaning] that components and structures are transported and then placed on the construction site, where there they will remain. We must also remember that it’s a process that must be very well thought out, analysed, and planned from the very beginning so that there are no bottlenecks and so that the benefits of this type of construction – the fact that it’s a high-quality, safe, and faster option that saves both time and money – are really taken advantage of.
Ver esta publicación en Instagram
What are some of the advantages over traditional construction?
With industrialisation, completion times are reduced, the quality is higher, there are fewer after-sales problems, fewer defects, fewer incidents, it’s more sustainable, it less noisy for the neighbours… There are many advantages, both for the client and for the contractor, for the professionals involved. It’s also important to understand that it’s possible to use industrialised construction for buildings of all shapes and sizes, and that, as it’s a process that is well thought out from the very beginning and considers everyone involved, it may take longer to complete the project, but in the end the overall time invested is shorter. In industrialised construction, everything is thought out in millimetres instead of centimetres, which is the case in traditional construction. Simply put, everything fits together better.
Ver esta publicación en Instagram
Compared to other European countries, there aren’t many examples of this construction model being applied in Spain.
It’s true that there are countries in Europe, especially in the north, that started working with this system earlier, mostly because their own climate often prevented them from working outdoors. It was incorporated later in Spain, but its use is on the rise, especially for single-family homes because it’s more complicated with high-rise buildings. But progress is also being made in that field, with multi-family buildings and the mechanisation of new components.
The mass production of construction elements such as bricks, beams, or slabs has always been present in construction. However, in industrialised construction these processes go a step further and whole building elements such as walls, floors, facades, and roofs, even stairs, balconies, wardrobes, kitchens, and bathrooms are now produced in factories. These components are still being developed and there is a shortage of skilled labour, but there is a growing need for more integrated and complete components to be installed in buildings.
Ver esta publicación en Instagram
Will industrialised construction become more prevalent in the coming years?
The industrialisation of building is the future, there’s no doubt about that. The question is how fast it will happen. I believe that in the next five years we will see more and more buildings with industrialised elements, with a part built using traditional construction methods and an industrialised part, like the façade or the bathrooms being made entirely in a factory.
More and more existing companies in the sector are taking the initiative and developing their own industrialised elements with the goal of integrating them on site. This is what Finsa has done [with the decision] to move towards CLT structures, which work very well. This type of offering is becoming more common for planners and developers, for whom there is an ever-growing range of industrialised solutions to integrate into their buildings. And they are asking for more.
Ver esta publicación en Instagram
What is the role of the public sector in the development of this model?
It’s very important that industrialised forms of building are a requirement for public housing because, in addition to its advantages, it also generates wealth. Why? Because it creates industry, generates demand, and may encourage the traditional builder to take the plunge.
Would you say that industrialised construction guarantees more liveable, healthy, and environmentally friendly spaces?
Yes. These are energetically efficient buildings, [and] the automated manufacturing of their components reduces material waste [and] debris, and it requires less transport, resulting in fewer CO2 emissions compared to the traditional model.
When it comes to refurbishment, is industrialisation a real alternative? How can industrialised solutions or systems be integrated into this type of project?
This is the most challenging area for industrialisation. [The Cluster has] a working group specifically for this. Producing components in a factory and then placing them in existing buildings, which have their own specificities, is a challenge because it clashes with the scalability and standardisation aspect of this methodology. But the need for refurbishment of the building stock in Spain is enormous and traditional solutions will have to coexist with industrialised solutions. Above all, it’s about solutions for roofs and façades that can increase insulation so that the building’s protective skin maintains thermal comfort on the inside no matter the conditions on the outside. These solutions have several advantages over traditional ones: they are quicker, they are less invasive for the neighbours who already live in the building and have to suffer through the renovation work [and] have less of an impact on their daily lives, and they promote circularity because they are elements that can be deconstructed and reused in the future.
What materials are most commonly used for these types of building solutions?
There is a bit of everything. The traditional choice is concrete, which has an environmental sustainability challenge that needs be dealt with. Another is steel, which has the advantage of being flexible in terms of being able to make components of various sizes, for different spaces, but there is also has the issue of price. Then there is wood.
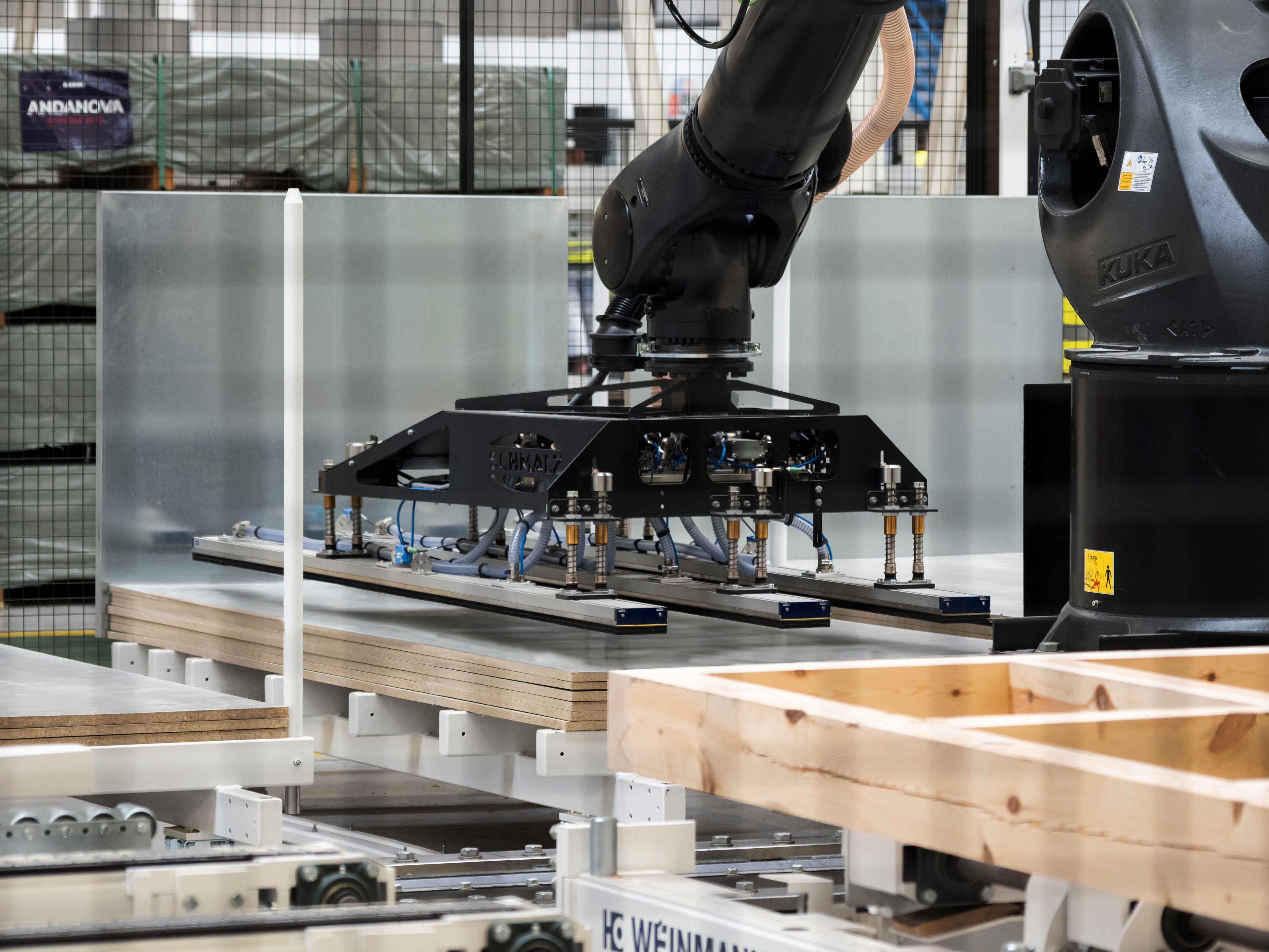
What does this material bring to the table? As a natural resource that is more sustainable and that offers more design possibilities, how does it benefit industrialisation?
Wood is a familiar material. Sometimes we talk about it as if it were something new, but it’s a classic that’s already evolved a lot. Whether it’s being used for structures, components, or industrialised elements, it has the advantage of maintaining its performance and being sustainable. Timber captures CO2 and its carbon footprint is negative. It does not emit carbon. Given that the construction sector is responsible for 30% of global emissions, we need building to be environmentally responsible. In addition, timber is a material that the customer quickly recognises as a comfortable one. If we want to be a standard-bearer for sustainability, wood is an essential element.
Ver esta publicación en Instagram
Let’s talk about the future of the sector. Which model is construction evolving towards in our country? Should we borrow from other models around us?
I believe our sector is a mature one. But it has also been estimated that Spain needs approximately 120,000 new homes every year. In this sense, coping with the construction of such a high number of homes, bearing in mind that there is a shortage of labour, will require alternatives to traditional construction. Industrialised construction is no longer in question.
As I said, the issue lies in the ability of those involved to do it sooner rather later. But I am convinced that in five years’ time we will see a substantial increase in this type of construction. More and more organisations want to innovate and go further. They know that they must invest in innovation because the future, where it’s heading, is taking over traditional construction methods. They are getting their act together and the business model is changing.
Ver esta publicación en Instagram
Finally, staying on the topic of the future and innovation, what is your assessment of the current state of digitalisation in the sector? Is the digital divide closing or are different areas of the sector moving at different speeds? In which areas is the transformation happening at a faster pace?
Our sector is not very digitalised, especially when it comes to the initial and final phases of projects. In the commercial area, the sales tools being used are already digital and virtual 3D models allow clients to view the interior and exterior of their home in different scenarios, with multiple combinations of different finishes, and more. And architects use BIM methodology. But when it comes to execution, that is, during the building process, or the integration of industrialised construction between those on site and the designer, the digital transformation has not yet been achieved, though a lot of progress has been made. The use of BIM at the actual building site and of technologies that can optimise performance is a developing field.